
„Um Vertrauen zu erlangen, muss man sich beweisen. Es ist die größte Auszeichnung für unsere Arbeit.“
Annett Barth,
Geschäftsführerin
DELTA BARTH Systemhaus GmbH
Wir steuern, digitalisieren und optimieren Prozesse – in mittelständischen Unternehmen ebenso wie in Schulen oder Behörden.

DELTA BARTH ist Profi in puncto Digitalisierung!
Teilhaben, wenn Ideen wachsen. Das ist unser Antrieb! Ob in mittelständischen Unternehmen, Behörden oder Schulen – mit IT-Konzepten aus dem Hause DELTA BARTH setzen Sie Ihre Pläne für Wachstum, Modernisierung und Weiterentwicklung um.
Über 35 Jahre am Markt
1990 gegründet ist DELTA BARTH heute eines der größten inhabergeführten Systemhäuser Sachsens.
Als Familienunternehmen mit über 65 Mitarbeitern stehen wir für Stabilität und fortwährende Innovation – Werte, die auch unseren Kunden wichtig sind.
Made in Germany
Als Hersteller der ERP-Software DELECO® steht DELTA BARTH für Unabhängigkeit, Kundennähe und Qualität auf höchstem Niveau.
Alle unsere Produkte in Software, Hardware, Schulung und Support durchlaufen ein strenges Qualitätsmanagement und erreichen so beste Ergebnisse.
Berater und Ideengeber
Ob bei der Einführung von DELECO® oder der Konzeption einer komplexen IT-Landschaft – erfahrene Projektleiter stehen Ihnen zur Seite.
Mit starken Impulsen bringen wir Sie voran. So begleiten wir den Fortschritt von mehr als 600 Kunden.
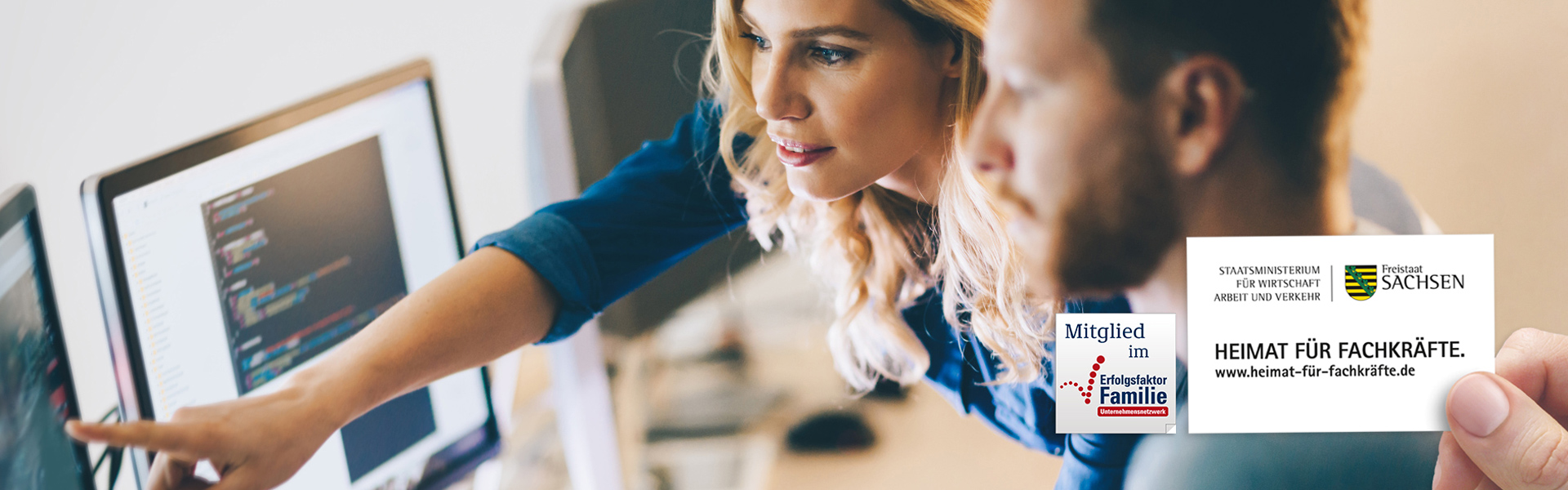
Karriere in der IT-Branche
Als einer der größten Softwarehersteller und IT-Anbieter der Region bietet DELTA BARTH eine Vielzahl abwechslungsreicher Jobs und interessanter Aufstiegsmöglichkeiten. Wollen Sie unser Team verstärken und unsere Zukunft mitgestalten? Erfahren Sie mehr darüber, welche Vorteile Sie als Mitarbeiter bei DELTA BARTH erwarten.
News
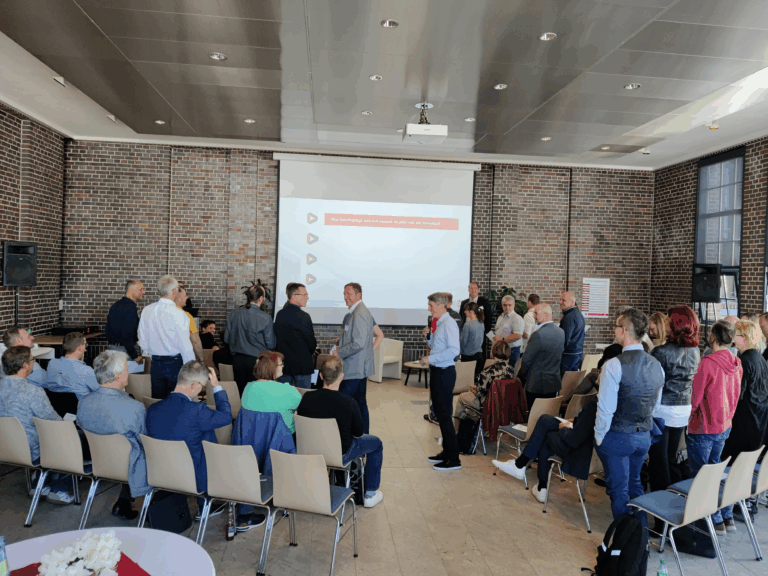
Rückblick auf den DELECO® Kundentag 2025
Ein herzliches Dankeschön! Ein herzliches Dankeschön an alle Kundinnen und Kunden, die unseren diesjährigen DELECO® Kundentag zu einem…
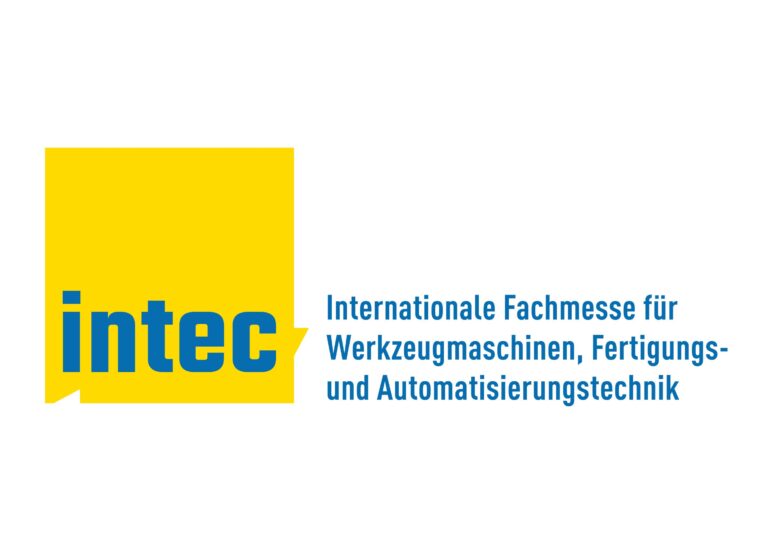
Sieben Unternehmen, ein Ziel!
Das Fertigungsnetzwerk präsentiert maximale Kompetenz “Made in Germany”. Limbach-Oberfrohna, Hartmannsdorf, Mülsen, Gelenau:Im Fertigungsnetzwerk bündeln sieben hoch spezialisierte Unternehmen…
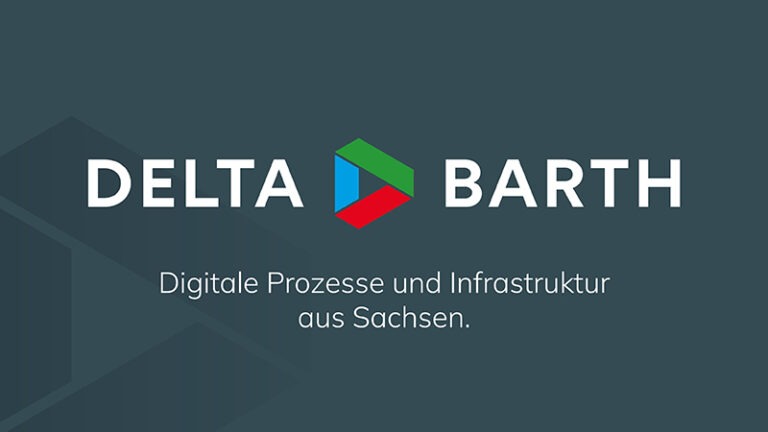
Wir feiern 35 Jahre – mit neuem Look, aber den gleichen Werten!
Neues Design, gewohnte Qualität und Verlässlichkeit. Wir feiern unser 35-jähriges Firmenjubiläum – ein bedeutender Meilenstein, den wir nur…